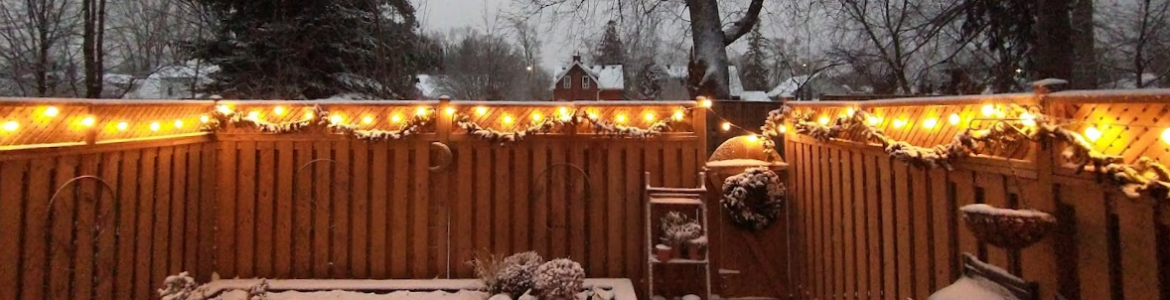
Case Study 8: Cold-Climate Hybrid Air-Source Heat Pump
Published Online January 2024
Executive Summary
Erik Janssen, a Research Scientist with the Sustainable Technologies Evaluation Program, shares his year-long experience with an air-source heat pump (ASHP) for space heating and cooling, alongside a heat pump water heater (HPWH) for domestic hot water, in his 3-bedroom townhome. Living in Mississauga with a family of four, Erik provides a detailed account of his motivations, challenges, and outcomes from this sustainable home retrofit.
Key Points:
- Motivation and Decision: Erik’s decision to switch to heat pumps was driven by a desire to reduce carbon emissions, lower energy bills, and leverage available incentives. The emergence of cost-effective cold-climate ASHP options and increasing gas prices expedited the decision.
- Building Envelope Considerations: Erik emphasizes the importance of considering building envelope improvements alongside ASHP installations, in his case, this included attic insulation and air-sealing. Though typically not a prerequisite for an ASHP, envelope upgrades can enhance overall comfort and ASHP utilization.
- System Configuration and Backup Heating: Due to electrical service constraints, Erik opted for a hybrid system with a 2-ton ASHP backed by a new gas furnace. He highlights alternative options for fully-electrifying the heating load within a constrained service.
- Equipment Selection and Noise Considerations: Outdoor noise considerations helped guide equipment selection and placement, seeking to reduce noise impacts on neighbors.
- Energy Consumption and Costs: Despite still having a gas furnace, Erik’s home has consumed no gas since the ASHP and HPWH were installed. The ASHP has managed the home heating needs in outdoor temperatures as cold as -16oC and the furnace was not needed so far. Electricity for the HPWH costed $13 per month on average, and the ASHP costed an average of $34 per month in electricity for the eight months where heating was used.
- Lessons Learned and Recommendations: Erik walks through several important considerations for heat pump installations like appropriate backup heating, ductwork limitations, heat loss calculations, and others. He suggests full electrification (i.e. disconnection from the gas grid) might be especially financially advantageous for homes with low design heat loss and few gas appliances because it eliminates fixed gas customer charges which can otherwise dominate the annual energy costs.
- Overall Satisfaction and Future Plans: Erik is happy with his chosen systems, citing lower upfront costs post-incentives, reasonable energy bills, and a lower carbon footprint. While contemplating a shift to full electrification for cost savings, Erik’s overall experience has been positive.
In conclusion, Erik’s case study serves as a valuable resource for homeowners considering ASHP technology, offering insights into the retrofit process, challenges, and the potential for sustainable cost-effective home heating and domestic hot water solutions.
Introduction
Greetings. I’m Erik Janssen, a Research Scientist with the Sustainable Technologies Evaluation Program (STEP) team. Having led the development of air-source heat pump case studies for our Smarter Home Heating Campaign (smarterhomeheating.ca), I’m now turning the spotlight on my personal experience. This case study delves into the details of installing and operating heat pumps for both space and water heating in my own home, documenting my journey throughout 2023 and the initial days of 2024.
Site
My family of four, including my wife and I as well as two children, live in a 70’s-era townhome in Mississauga with attached neighbours on either side. The total conditioned floor area across a finished basement and two stories is approximately 1,600 ft2. The estimated design heat loss from our energy audit was 23 kBTU/hr. I purchased the home in 2019 and inherited an inefficient atmospheric vented gas tank water heater and a 95% efficient gas furnace. These are the only gas loads in the home. With both of these systems and the A/C nearing 15 years old by early 2023, the time had come for more energy efficient replacements.
Rationale
Having worked in and around heat pumps for more than a decade now, I had full confidence in the technology and I knew this was how I wanted to heat and cool my own home. My motivation extended beyond personal preference. It was a conscious choice to reduce my family’s carbon footprint, contributing in our own way to the fight against climate change. We also sought to reduce our home energy consumption and bills. The available incentive programs, the emergence of new lower-cost cold-climate air-source heat pump (ASHP) options, and increases in the cost of gas all helped to expedite the decision to make the switch.
Building Envelope
Building Envelope Improvements and Heat Pump Retrofits
If you are thinking about a heat pump, it is also a good time to think about other opportunities for improving the energy efficiency of the building envelope. In my case, the attic insulation and air-sealing were the low-hanging fruit. The home has windows from the early 90’s that are due for replacement, but that is still on the to-do. Envelope improvements can help with heat pump sizing and utilization, but also improve your comfort.
However, while envelope improvements are certainly important, I think it is an overstatement to say that envelope improvements are normally a pre-requisite for an ASHP install. The window of opportunity for most people to install an ASHP is when their existing furnace or A/C (or both) is at end-of-life, and that’s the time to install one whether there have been envelope upgrades or not.
I always recommend back-up heating (whether gas or electric depending on your home and your motivations) not because heat pumps have a problem with the cold, but rather, because the heat loss estimate for your home is just that, an estimate, and I don’t think it is wise to try to cut it too close in terms of ensuring you have adequate heating and home comfort. If you’re in a situation where you need to install an ASHP without yet having thought about the building envelope, it will likely just mean greater reliance on back-up in the meantime.
Attic Insulation
In early 2022, the loose fill fiberglass insulation in the attic was removed and replaced with new loose fill fiberglass insulation due to a mold issue that has since been addressed. The new insulation added some additional thickness, it is now about 18” thick total and corresponding to about R50, but I plan to still top it up myself. The condo corporation handled the insulation replacement. In hindsight, I ought to have encouraged them to use cellulose because it is more environmentally-friendly.
Air-sealing
While the insulation was out of the attic during the replacement, I took the opportunity to improve the air-tightness of the home. I did this work myself, basically following the recommendations in [1]. I taped the vapour barrier seams, sealed over the light fixtures with plastic, and used expanding foam in any cracks/openings from wall plates, the plumbing stack, and around the perimeter. I used high temperature caulking around the water heater exhaust travelling up through the attic. The cost of supplies was less than $100 and it was approximately a day’s work.
Educate Yourself
A recommendation that applies to both building envelope improvements and heat pump installs, is to educate yourself on best practices for the work your contractors are doing. As an example, prior to the attic insulation replacement I read up on attic insulation best practices [1] and included in that was installing airflow baffles to prevent the loose fill from clogging the soffit (which is the air intake for attic ventilation). The contractor did not do this initially nor did they blow in the required thickness of insulation. Had I not caught the ventilation issue, there could have been mold issues again down the road. We’ve listed some of the best practices for heat pump sizing and design on our website. [2]
Getting Ready for the Heat Pumps
Electrical Panel and Service
My existing electrical service panel was original to the home and used fuses rather than breakers so, for obvious reasons, I was wanting to replace it. It was a 60 A panel. The electrical utility said that an upgrade to 200 A was not feasible. The service leading to my home was suitable for 100 A so the new breaker panel maximum capacity was then also 100 A.
My electrician looked at what I wanted to do – an ASHP for space heating and a heat pump water heater (HPWH) for domestic hot water – and concluded that, on the new 100 A panel, I could do a HPWH and a 2-Ton ASHP but there would not be enough capacity on the panel for electric resistance back-up heating. I confirmed what the electrician had said about the lack of capacity on the panel using an online calculator that implements the calculations in the Canadian Electric Code used for electrical panel sizing.
Back-up Heating Requirements
From discussions with my contractor and my own calculations using NRCan’s Air-source Heat Pump Sizing and Selection and Toolkit, [3] we believed that the 2-Ton cold-climate ASHP would be able to handle the full home heating load down to around -15oC but during the very rare occurrences where it gets colder, I would likely need back-up.
The solution we arrived at was a hybrid system that backed-up the ASHP with a new gas furnace since the gas furnace doesn’t require additional electrical capacity. My goal was to reduce carbon emissions from gas as much as possible, but we needed to work within the constraints of the home. We reasoned that the back-up would only need to operate for a limited number of hours per year, and in some years not at all, so it seemed an acceptable solution that would make ensure my home was always warm while still nearly eliminating my gas consumption.
Alternative Solutions for Working Within 100A Electrical Service
In hindsight, I’ve learned of other options that would have allowed me to fully electrify the home. For example, there are smart switches that allow your electric back-up to share the same circuit as another large load (like the dryer) and only ever allow one load to operate at any given time. [4] Another option, the one I would have likely gone for (and still may), is to replace my basic electric dryer with a condensing dryer (a heat pump dryer) that has much lower current requirements, therefore “making space” on the electrical panel for back-up electric resistance heat.
Lead Time
The electrician did the panel upgrade and installed the two new circuits for the ASHP and HPWH. The new circuits were about $500 each for materials and labour. The panel upgrade had a couple months lead time because we needed to coordinate with electrical utility so that they could come and cut the power to the home so that the electrician could safely replace the panel. It’s a good lesson that, in general, ASHP installations may demand more lead time than conventional equipment installs – so don’t wait until your equipment breaks down to start planning for an ASHP.
Equipment Selection
New ASHP Options
For most of my time watching the industry, it seemed that the available options were on the extreme ends of a cost/performance spectrum with not much in the middle. However, over the past few years, a new class of equipment has emerged and this was especially interesting to me. This new “middle-of-the-road” class of equipment struck more of a balance between upfront cost and performance.
There are now inverter-driven variable capacity options, including cold-climate options, that have a lower upfront cost for those on a budget. There are also now variable capacity cold-climate options that can work with both new and existing furnaces – and this was a major development. I chose one of these “middle-of-the-road” options for my home. We’re not sure it’s our “forever home” but had we been sure, we may have opted for a more premium model.
Home Heat Loss Estimate
We selected a 2-ton variable capacity cold-climate ASHP backed up with 40 kBTU/hr furnace. The former furnace had a 70 kBTU/hr heat output – about three times the heat output that would really ever be required! This illustrates an important point for heat pumps that the industry overall needs to continually improve on, namely, developing good heat loss estimates of homes and right-sizing equipment to the home heating needs.
The size of the existing equipment in a home really offers no meaningful information about the heat loss of the home because conventional systems are quite often significantly oversized. NRCan recommends that contractors perform a heat loss calculation compliant with CSA F280-12. One of the things my group is currently working on is a tool that estimates heat loss estimates from historical energy consumption. There are different approaches but in general, a good heat loss estimate is the foundation of heat pump sizing and selection. In my home, we looked at both the historical energy bills and the results of the energy audit to estimate the heat loss.
Costs and Rebates
Upfront costs (installed; pre-tax; pre-rebate; including new circuit) including both the ASHP and new furnace were about $13,500. This ASHP qualified for the maximum Enbridge HER+ heat pump incentive of $6,500 because it was a cold-climate model that maintained a required level of heating output and efficiency in very cold temperatures.
Having a cold-climate system was important to me because it meant that the heat pump could continue heating the home into very cold temperatures. I also received a no-interest loan through the Canada Greener Homes Loan. After considering the incentives and the loan, the furnace-ASHP system was less costly than a conventional furnace-A/C system. At the time of writing, the future of heat pump grants is uncertain but it is important to note that we have profiled other homeowners that have gone forth and done cost-effective ASHP installs without the support of grants. [5]
I installed a 60 gallon HPWH as well. The HPWH cost about $6,250 (installed; pre-tax; pre-rebate; including new circuit) and qualified for a $1,300 incentive and no-interest financing. Ater considering both of those incentives, the heat pump water heater started to approach the cost of a good tankless gas water heater. Overall, with the incentives, I paid less total for this equipment than I otherwise would have had to for conventional replacements my furnace, A/C, and water heater.
Considering Outdoor Noise
One of the key things I considered when selecting equipment and planning for the retrofit was outdoor noise. The City of Vancouver, which has stringent noise by-laws (note that air-conditioners are less common there than here in southern Ontario), has some good general guidance and much of it is also useful for ASHP installations in Ontario. [6]
The dB Rating
It starts with choosing equipment that has an outdoor noise rating (the “dB rating”) that is appropriate for where you are putting it. The Vancouver document says around 60 dB is considered quiet. Mine has a rating of 62 dB and it is variable-capacity, meaning that it modulates its heating output, having a quieter compressor and outdoor fan when at part load, and also having a softer less-noticeable start-up noise. Units are also available with a dB rating in the low-50s (the sound level of a quiet office). Conventional A/C units that many of us are used to can easily exceed 70 dB (the sound level of city traffic) and can also have a jarring noise on start-up.
ASHP Noise vs. A/C Noise
Outdoor noise considerations are especially important because the ASHP will be on frequently throughout the winter. However, in comparison to the noise from A/C, it’s also important to note that the ASHP is making outdoor noise when people are generally indoors (because it is cold outside) so I think, if the right ASHP is selected, it is less of a nuisance overall than the A/C units we are already used to. In the summer, I try not to use A/C and like to sleep with the windows open. On warm summer nights, I fall asleep the sounds of basic A/C basic banging on and off around me. If neighbours switched to properly selected and sited inverter-driven ASHPs then I think it would be overall a benefit to the sound landscape of neighbourhoods rather than a detriment – simply because it will be much quieter outside when we are outside enjoying nicer weather.
Siting the ASHP
The second thing to consider was proximity to the property line. I made sure my ASHP was installed centrally on my home in the backyard to put it as far away as possible from my neighbours on either side. Backyard installation is often a good idea in detached homes as well. If an ASHP is installed on the side of a house directly adjacent to a window on the neighbour’s home, it can create noise problems for the neighbour. I also made sure to put it on a stand rather than a wall-mount to limit vibrations and noise transfer.
Noise Levels So Far
My installation has a bit of quirk in that, with the limited space I have in my backyard, I have a canoe mounted directly over top of it that I think acts as a sound barrier. If you’re outside and right next to the ASHP, there is definitely a loud whooshing of air from the outdoor fan and a quiet hum from the compressor (but it again, it is quieter than a traditional A/C). Once you step inside the home with closed windows, the outdoor unit is generally hard to audibly detect on the main level, and in the second-floor bedrooms directly above the heat pump, it is generally just barely noticeable or not noticeable at all.
In more extreme cold, say colder than -10oC, it is on more frequently at its maximum capacity. It becomes more noticeable in the above bedroom and in adjacent areas of the main level, albeit still quieter than an A/C unit. It’s acceptable to my wife and I, and my neighbour reports that that he can’t hear my ASHP operating when he is inside his unit.
Figure 1. My heat pump is quite happy heating the home on a cold January day at -14oC.
Remember the Outdoor Unit Blows Air
Mine is a side-discharge unit. When it is on, it blows air out over the deck in my small yard. This is important to be aware of in the event it impacts the usage of the outdoor space. It’s not an issue in my home because we don’t hang out on the deck in the winter, and if it is cooling the home in the summer (which isn’t very common) we’re generally not outside on the back deck. Even if we were, we could orient the deck furniture accordingly.
After the Installation
The installation went off without a hitch, aside from the fact that my old water heater died and my contractor was thankfully able to bump up the timelines for the installation.
Indoor Noise
After the equipment was installed, there were a few issues that we needed to sort out. The first issue was that the noise from indoor airflow was substantially louder than the noise from the previous furnace. Unlike some of the premium ASHP options that have a modulating indoor fan that is mostly operating at part-load (and quieter), when my ASHP comes on, it comes on at a single indoor fan speed. In cold conditions, it was on often and it was louder indoors than I preferred.
It turned out that the furnace dip-switches needed to be re-configured to get an appropriate airflow for a 2-Ton ASHP (they had been set at something more appropriate for 3-Ton, so about 50% more airflow than needed). The noise was therefore a result of the fact it was pushing more airflow through the ductwork than was needed. Adjusting the airflow brought the noise down to a much more acceptable level.
Thankfully it quickly came to a positive resolution, but this experience made it clear to me how important it is for contractors to work within the constraints of the existing ductwork when sizing ASHPs. Trying to push too much air through too little ductwork might really sour the user experience with a heat pump because of the noise it creates, and also possibly cause equipment issues. Again, this issue is also mitigated for units that modulate the indoor fan. Different initiatives are also underway to help contractors ensure they are effectively working within the ductwork airflow capacity.
HPWH Noise
There were also noise issues initially with the HPWH. It was generating a high-pitch electronic hum that could be heard throughout the whole home, even in the second-story bedrooms. We needed to turn on electric resistance back-up heating and turn off the heat pump function because the noise was too much. Oddly enough, it turned out that the issue was with the little axial fan in the HPWH unit. My installer was quick to help get that part replaced on warranty, and then there were no issues with noise.
You can hear the water heater when you are in the basement room that is directly adjacent to the mechanical closet. It’s not quiet but it sounds comparable to when the indoor blower is on for the ASHP. It’s not audible anywhere else in the home. The water heater has an app that allows us to schedule it, so I just adjusted it to be off for a few hours every evening when we are typically using the basement living space, and it works out just fine from a noise perspective.
HPWH Cool the Space They Are In
One of the key things to note about the heat pump water heater is that it uses heat energy from the ambient space around it to heat water. This actively cools the space it is in and potentially offers some dehumidification. My basement mechanical closet has a louvred door to exchange air with the adjacent living space and that space is noticeably cooler after the unit has been running. This is actually a blessing in the summer months – free A/C! In the winter months, we accept it and the scheduling of the unit helps as well.
If it really became an issue for us there are different options. We could adjust the setpoint schedule to allow time for the cooling it generates to dissipate before we use the space. We could utilize the integrated electric resistance heater to a greater extent, but this would sacrifice energy efficiency. It is also feasible to duct the supply of the ASHPWH into the return drop of the furnace which would spread the small amount of cool air from the HPWH out across the home and, when the heat pump was on, mix it with warm air from the heat pump. For us, it is acceptable as is for now and we haven’t taken these other measures.
Overall Experience with The Systems
We’ve never been without hot water when we wanted it. The level of indoor comfort provided by the heat pump is comparable to the previous furnace. Both maintained the thermostat level without large temperature fluctuations. The heat pump just needs to operate at a lower heating output for a longer period of time to do it.
Data
No Gas Consumption
The home has consumed no gas since the heat pumps were installed. I now submit my gas reading to Enbridge monthly and every month it is the same number – 13,686. I know the heat pump is therefore good to keep the indoor temperature at 20oC to 21oC in outdoor temperatures as cold as -16oC, which is as cold as we’ve gotten. That also means I know the ASHP is good to handle greater than 95% of the annual heating load for the home fully on it’s own. We were close with our initial estimates of how much heating the ASHP could do but we’ll need colder temperatures than what we’ve had to determine when it will fall short.
Total Electricity Consumption
The total monthly electricity for my home from Feb 2023 to Jan 2024 is shown in Figure 2. I am on tiered electricity. Even with the HPWH and ASHP, I generally do not exceed the limits for the lower tier, which is 1,000 kWh for winter (Nov. 30th to April 30th) and 600 kWh for the rest of the year. The only month where I went slightly into the upper tier is November, and even then, by only a small amount.
Figure 2. Monthly total home electricity consumption for one year after the ASHP and HPWH installations. This includes all electricity loads in the home.
Monthly Electricity Consumption Breakdown
In Figure 3, I’ve plotted the HPWH consumption (measured in the HPWH app) and the estimated ASHP consumption for heating. I estimated the ASHP consumption as the sum of the 2022 monthly consumption (as a baseline) and the HPWH consumption subtracted from the 2023 total monthly consumption.
Figure 3. Monthly electricity consumption for the ASHP heating and HPWH. I’ve neglected cooling in this figure because we don’t use a lot of cooling. The HPWH peak in February was due to the noise issue that was fixed.
Electricity Costs
In Figure 4, I’ve determined the monthly cost of HPWH and ASHP by multiplying the consumption by the current marginal electricity rate for lower tiered electricity. I determined the rate from the Ontario Energy Bill Calculator Portal. [7] Using the Calculator, it is possible to enter consumption at two levels (for example 400 kWh and 500 kWh) and determine the total cost of the resulting bills including all taxes, fees, and rebates (which can otherwise be hard to sort out). The difference in the bills divided by the difference in consumption is the all-in marginal electricity rate. The current marginal rate for lower-tier electricity determined using this approach is 13.0 cents/kWh. The average monthly cost to run the HPWH is $13. The average monthly cost for the ASHP over the 8 months with some level of heating is $34, although it peaked at $53.
Figure 4. The monthly operating costs are shown for the ASHP and HPWH.
Space and Water Heating Cost Annual Breakdown
A total breakdown of the energy costs for space and water heating is shown in Figure 5. It has 3 components: (1) the electricity for the ASHP; (2) the electricity for the HPWH; and (3) the fixed customer charge for the gas utility to maintain an account (~$25 per month). Recall that I consumed no gas over the one-year period I am looking at, so gas consumption costs aren’t included in the chart, but I still have a gas connection for that rare day I need to use the furnace when it gets extremely cold. Maintaining that gas connection has a fixed cost. The total costs from all components for the year was $732 and 41% of that, the largest component of the total costs, was the fixed gas customer charge despite the fact that I actually needed no gas this past year.
Figure 5. The total annual costs for space and water heating is shown. It includes the electricity consumption of the ASHP and the HPWH, and the fixed gas customer charge for the gas connection (despite using no gas).
Cost Savings
Unfortunately, I don’t have good baseline gas data to determine the extent of any savings or confirm definitively if there was a savings. The reason is that my gas meter is behind a locked gate in the backyard and nearly every historical bill prior to the heat pump install is based on estimated gas consumption with only the occasional actual meter reading. The upshot being that I can’t decipher what my weather normalized baseline gas consumption is from the data I have directly available.
My gas historical gas consumption is definitely less than 1,000 m3 per year but I don’t have the data for how much less nor would I have enough information to correct for weather. If I had to hazard a guess, it would be that, at current rates, I don’t think there is a huge difference in the total cost I am paying for space and water heating between what I had before and what I have now.
If I wanted to maximize the cost savings, while still maintaining a gas connection to the home, then I could consider the “smart-switching” approach that we explored in [8], which seeks to choose furnace or ASHP in real-time based on whichever option is expected to provide the lowest cost heating. We determined that while there is still room for improvement, the approach has merit from an operating cost perspective. For now, I’m content just to reduce gas consumption as much as possible.
Lessons and Recommendations
Overall, I think the data tells two important stories:
- The operating cost to heat my home with the ASHP and hot water with the HPWH pumps were very reasonable. Hot water heating for the year was $160 total, and space heating was $271.
- For homes like mine, with a relatively low design heat loss and few gas appliances, it can make financial sense to consider full-electrification and disconnect from gas entirely.
There is lots to unpack there but, from a strict financial perspective, the data shows that the fixed gas customer charge can end up being the largest component of the overall energy costs for space and water heating in homes with a small design heat loss. Fully electrifying can avoid that fixed cost.
If I fully electrified my home using one of the options I mentioned, my cost for this past year would have been $431 instead of $732. Fully electrifying would have been close to comparable on upfront cost. The heating system would have been cheaper because I’d lose the furnace and have an air-handler instead, but then I would have needed to spend a bit to ensure I stayed within the limits of the 100A panel (for example, with a dryer upgrade).
As part of our overall Smarter Home Heating Campaign, we’ve summarized in a separate document some of our key learnings from 2-years of consultations with homeowners, contractors, energy advisors, and industry experts. [2] In this case study I wanted to show how these considerations impacted my own retrofit.
Final Thoughts
Over the past year, we’ve been happy with the systems we selected. After incentives and rebates, the combined system costs were lower upfront than the conventional options I may have otherwise chosen. The energy bills are reasonable. We have hot water when we need it. The heating system keeps the home at the desired set-point even into very cold outdoor temperatures.
At the same time, I’ve consumed no gas and reduced my home’s carbon footprint. When we do the needed window upgrades, I’m confident that I will be able to continue to use the ASHP as the source for heating for temperatures that are even colder than -16oC since the energy audit estimated that windows accounted a third of the heat loss.
However, when I look at what I am spending on the fixed gas customer charge in proportion to total space and water heating costs, I would have chosen differently knowing what I know now and sought to fully-electrify the home simply because it would yield the lowest operating costs. I may still make this change but for the time being, my experience has been very positive.
People may opt for a hybrid system for different reasons. In my case, it was a technical reason related to the electrical service. For those going the hybrid route, I would advise that they consider sizing their ASHP such that it can handle as much of the annual hearting load as possible within the constraints of the home and budget. For those in Southern Ontario, like myself, I think a good target might be to try to ensure that the ASHP can heat in the home in -10oC or colder since about 90% of the annual heating load is above this outdoor temperature.
Having an ASHP that can do the majority of the annual heating load can help optimize savings if you want to opt for a smart-switching control approach [8], and it also prevents you from being locked-in to gas if the utility cost landscape changes in the future. In other words, having an ASHP that can handle the large majority of the annual heating load will give the greatest flexibility moving forward.
References
[1] Natural Resources Canada. Keeping the Heat In. https://natural-resources.canada.ca/energy-efficiency/homes/make-your-home-more-energy-efficient/keeping-the-heat/15768
[2] Sustainable Technologies Evaluation Program of Toronto and Region Conservation Authority. Quick Tips for a Home Air-source Heat Pump Retrofit. https://sustainabletechnologies.ca/app/uploads/2023/12/Homeowner-Guidance_v2.pdf
[3] Natural Resources Canada. Air-source Heat Pump Sizing and Selection Toolkit. https://natural-resources.canada.ca/maps-tools-and-publications/tools/modelling-tools/toolkit-for-air-source-heat-pump-sizing-and-selection/23558
[4] Passive House Alberta. Electrification of Homes Without an Electrical Service Upgrade. https://www.passivehousecanada.com/wp-content/uploads/2023/08/20231026-Electrification-without-a-service-upgrade-report.pdf
[5] For example, see Case Study 6 or 7 on smarterhomeheating.ca.
[6] City of Vancouver. Heat Pumps and Noise: A Neighbourly Installation Guide. https://vancouver.ca/files/cov/heat-pump-noise-guide.pdf
[7] Ontario Energy Board. Bill Calculator. https://www.oeb.ca/consumer-information-and-protection/bill-calculator
[8] Sustainable Technologies Evaluation Program of Toronto and Region Conservation Authority. London Residential Smart Hybrid Heating Pilot: System Performance Analysis. https://sustainabletechnologies.ca/reports/london-residential-report/