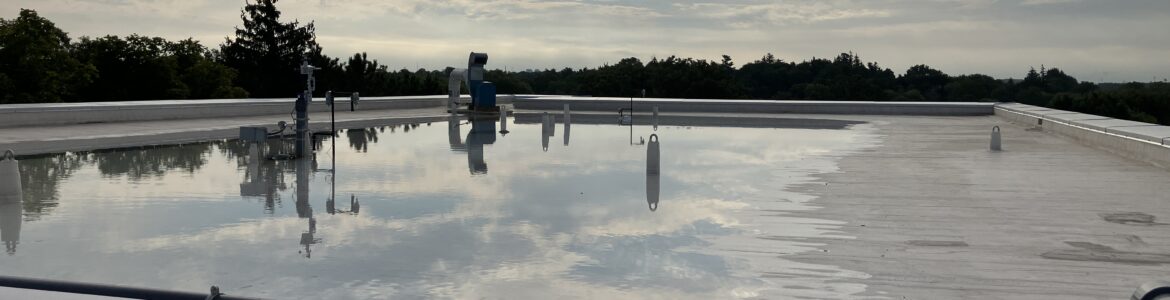
Smart Blue Roof Case Study
Prepared by: Credit Valley Conservation
Blue Roof System Overview
The smart blue roof (SBR) system at Credit Valley Conservation’s (CVC) head office in Mississauga, Ontario, is an innovative retrofit designed to capture, store, and reuse stormwater. The blue roof system reduces strain on the storm sewer system, mitigates the risk of downstream flooding, and provides a potential benefit in energy savings through evaporative cooling of the building. The project integrates rainwater harvesting (RWH) with intelligent controls and sensors to enable real-time water level management, greywater reuse, and reduced environmental impact.
Installed on the existing low-sloped concrete roof structure of the building, the SBR stores stormwater temporarily on the roof surface, which is coated in a double-ply, seamless, waterproof membrane. Modulating control valves allow water to pond on the roof when closed or drain to the basement cistern when open. The stored water is filtered, disinfected, and reused for non-potable applications such as toilet flushing (Figure 1). The system uses a programmable logic controller (PLC), level sensors, and modulating control valves to monitor and optimize water reuse and evaporative cooling.
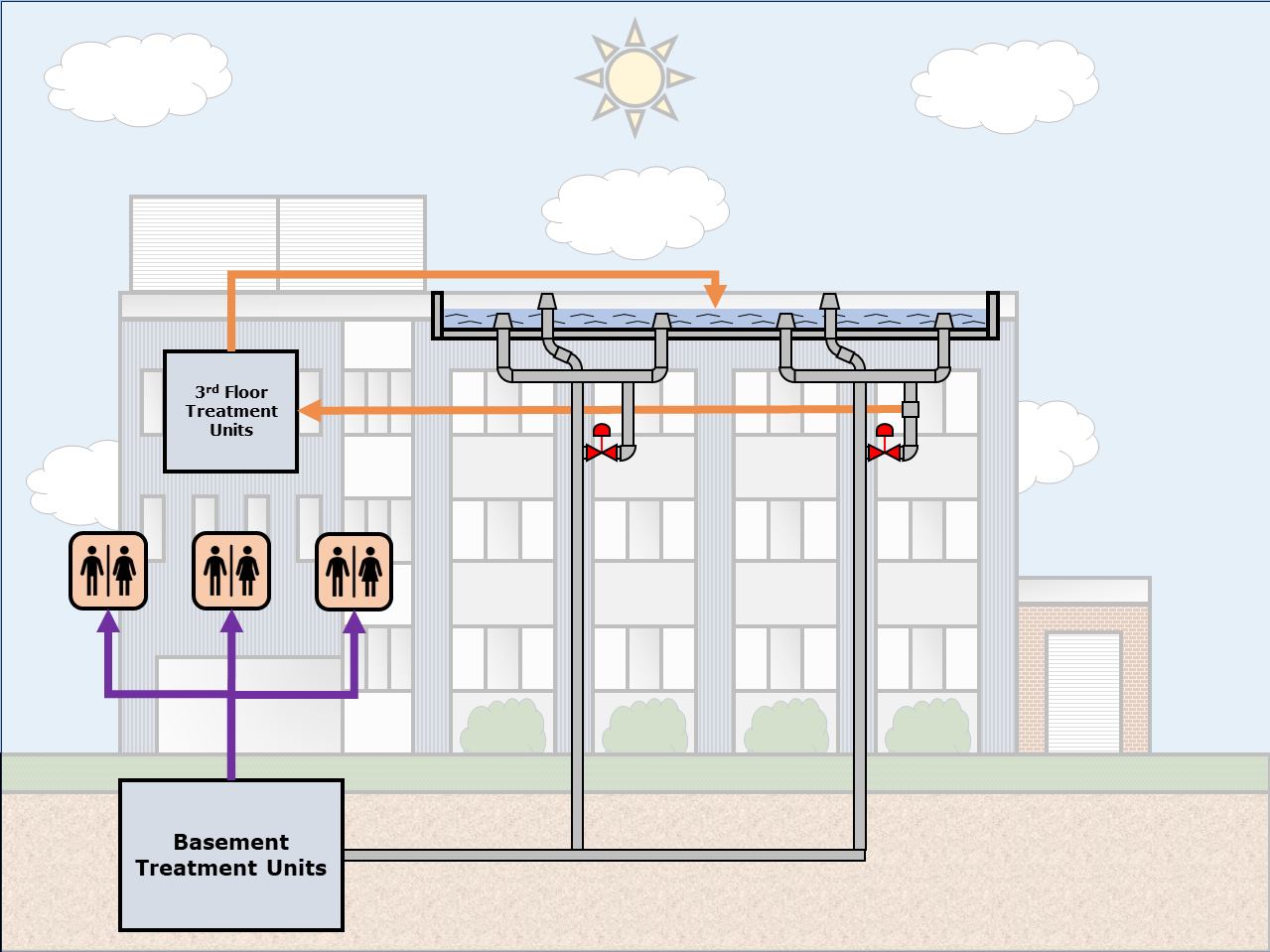
SBR Performance Data
SBRs offer significant benefits for stormwater management by reducing stormwater volumes and peak flows, extending the lifespan of grey infrastructure, and reclaiming urban land. Toronto Metropolitan University (TMU) modelled a 605 ha Cooksville Creek subcatchment that drains to the Saigon Stormwater Management Pond, which was design to capture approximately 250,000 m3 of stormwater. The total roof area suitable for blue roof retrofitting within this subcatchment was estimated as 1,465,959 m2. The analysis showed that 100% SBR adoption with 150 mm storage depths could remove up to 198,300 m³ of stormwater during a 100-year event.
TMU also modelled a 16.7 ha industrial-commercial area in the Greater Toronto Area characterized by high imperviousness, looking at the area as six study sub-areas. Due to increased development, this region has increased imperviousness compared to design conditions. The study demonstrated that existing storm sewer pipes are undersized in some sub-areas for the 5-year storm, and in all sub-areas for the 10-year storm. With projected 2050 rainfall scenarios, none of the existing systems would be able to handle storms beyond the 2-year event. The addition of SBRs would allow all sub-areas to manage projected 2050 5-year storm conditions and reduce or eliminate overflows for 10-year storms, deferring or avoiding major upgrades.
Additionally, the design of CVC’s blue roof system is complex, and analysis of simpler, more cost-effective blue roof options should be explored further. Design costs are also expected to be higher to retrofit a building than they would be to implement SBRs into new builds. Another potential cost saving comes from the City of Mississauga’s stormwater credit program, which reduces stormwater charges by up to 50%, if landowners’ properties contribute to peak flow reduction, water quality treatment, and volume capture.
While SBRs provide benefits through cooling and water reuse, net energy impacts depend on the specific system design and operation. Over the monitoring period of August 17 to October 30, 2024, the total rainfall volume recorded was 68,089 L. CVC’s SBR captured all rainfall during the monitoring period, including all rainfall from the two 100-year storm events on July 16 and August 17, 2024. By ponding water on the roof surface (Figure 2), CVC reused 43,388 L of water for toilet flushing. This offset 47,727 L of municipal supply, accounting for municipal treatment and distribution water losses. 20,364 L of water was also evaporated from the roof, contributing to evaporative cooling of the building, and 2,845 L was released as dry weather flow, relieving pressure on the storm sewer system during high intensity events. The SBR dissipated 12,764 kWh through evaporative cooling, reducing air conditioning energy needs by an estimated 4,300 kWh. However, water treatment and recirculation systems used for maintaining water quality consumed significant energy, resulting in a net energy increase of 860 kWh in the pilot project. Reducing recirculation and treatment could enhance GHG savings. Further monitoring is required to refine energy usage and reduction estimates, and water quality sampling is ongoing to determine specific water treatment needs.
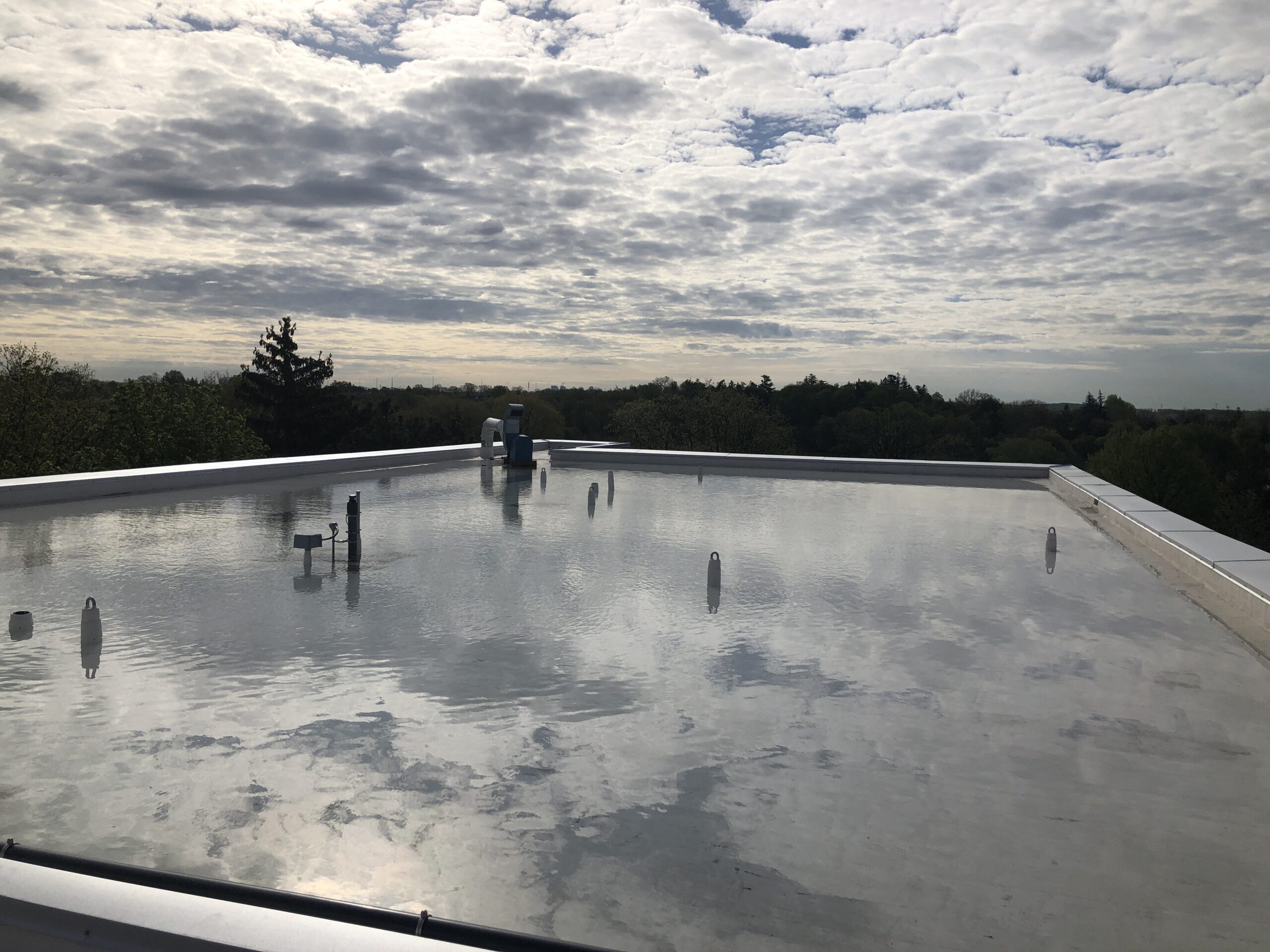
Challenges and Lessons Learned
Communication with contractors, vendors and stakeholder groups
Strong communication between contractors, vendors, and stakeholders was essential throughout the project. The involvement of multiple parties, including structural engineers, municipal partners, and internal CVC staff, made early coordination vital. Securing an exemption to the Ontario Building Code to store water on the roof for more than 24 hours required proactive engagement with the City of Mississauga and a clear demonstration of health risk mitigation strategies such as chlorination and recirculation. Clear communication was also required to explain and mitigate disruptions during construction. Additionally, it was important to get confirmation that warranty requirements for building materials, such as the polymethyl methacrylate roof membrane, were being met to avoid potential risks and liabilities.
Design modifications
As a retrofit, the project revealed concealed conditions at CVC’s head office resulting from discrepancies between the original building drawings and the actual structure of the building. Thinner-than-expected roof insulation and concealed infrastructure required real-time design adjustments, such as rerouting piping and lowering the location of modulating control valves to floor level (Figure 3). Budgeting for extra time and resources in the planning process can help to mitigate these challenges.
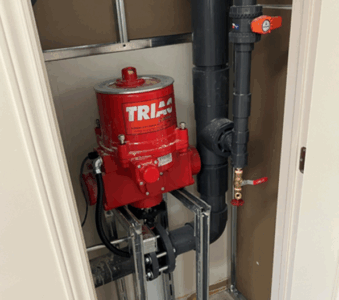
Water quality and chlorination
Several lessons were learned regarding water quality and chlorination considerations. Challenges were encountered when calculating the appropriate volume of chlorine needed, automating the chlorination process and addressing health and safety concerns. System upgrades were completed to enable an automated chlorination process, including the addition of a solenoid valve to control chlorine input, and a sampling valve to test chlorine residual concentrations. To address safety concerns, the rooftop HVAC intake was also adjusted to prevent chlorine vapors from corroding the system and avoid odors circulating throughout the building.
Data collection and transmission
The SBR’s monitoring and automation requirements underscored the importance of selecting appropriate data systems. The use of a PLC required custom workflows to transmit sensor data to CVC’s cloud storage and WISKI database. Challenges such as international IP restrictions and the lack of backup power during outages highlighted the need for system redundancies, like SD card logging and backup power systems.
Recording the performance of operation tasks was essential for data analysis and maintenance planning. Recording manual water level measurements and taking detailed notes when water was manually drained from the roof allowed CVC and TMU staff to complete data validation and post-processing. Recording the frequency of system maintenance was also informative for scheduling operations and maintenance tasks in future operating seasons.
Maintenance and materials
Material selection is critical for long-term performance. Aluminum roof drains oxidized prematurely, reinforcing the need for corrosion-resistant materials like stainless steel. Pressure conditions should be carefully monitored and controlled to prevent ruptures or equipment failure. Redundant safety measures should be implemented, including a casing around the chlorine canister to prevent spray in the case of rupture, an upstream pressure gauge to detect air within the pump, and pressure gauges around the micron filters to indicate cleaning or replacement needs. Troubleshooting was required to resolve system faults and warnings, such as adding a cool touch valve to prevent the UV treatment lamps from overheating.
Conclusion
The SBR project demonstrated that adaptive, intelligent stormwater systems are not only feasible in retrofitted buildings but also provide measurable benefits in water conservation, peak flow reduction, and storm sewer system resilience. The project’s success was reinforced by positive feedback from municipal partners, who highlighted its value in climate adaptation planning. By documenting system performance and operational insights, CVC created a model for future implementations. Lessons from this pilot, ranging from data management and stakeholder coordination to chlorination and maintenance, will inform and mitigate risks for similar projects.